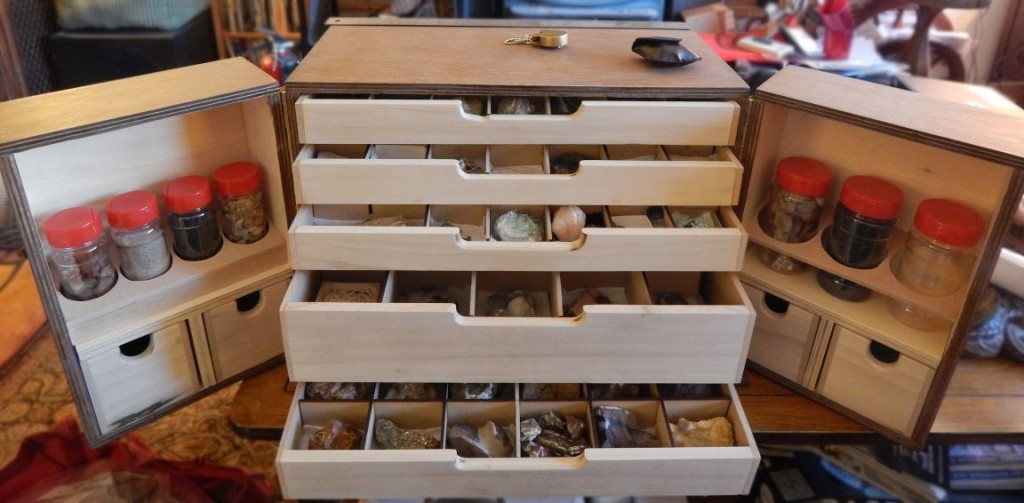
When Christmastime was rolling around, I had some gifts (almost all of them, I guess) that would require access to Schenk’s laser cutter. But then he was called out of town at the last minute. Oh no! Fortunately, his wife was kind enough to allow me to stop by and finish my gifts in time for Christmas. When I was walking out the door with my arms loaded with gift parts, I told her that I would design her something worthwhile.
The BPAL Box for Isaac’s wife Cyl. The Needlepoint Box for Pete’s Wife Sarah. I decided to continue the tradition of box-making tailored to the recipients specific hobby. Something that makes them unique. For their wedding centerpieces last year, Lisa deployed some of her finest mineralogical specimens to support the rustic, natural theme of their reception. But visiting their home a few months later, I saw some of them in a bucket. That just won’t do.
I doodled a couple ideas for what I wanted the box to look like. I knew I wanted shallow sample trays, so each specimen would be easily visible and accessible. I wanted doors on the front so that the trays wouldn’t slide out during transport. If the doors were deep enough, I could make space for smaller containers for sands, soils, and agates, along with specimen maintenance tools like brushes and loupes.
Withe dimensions roughed out on paper, I translated the design into Sketchup so that I could get some hard numbers.
I didn’t want visible screws, so this box marked my foray into plate-joinery. I received a plate joiner as a gift last year, but haven’t had an opportunity to use it. The box was going to have rocks in it, and I didn’t want it coming apart when moving it.
The carcase is made of 1/2″ sandeply joined with biscuits, and the trays are Poplar fronts with 1/4″ MDF joined using my 17-gauge pin nailer. After assembling the third tray, I finally got the idea that the MDF wouldn’t split if I pinned it closer to the middle of the boards. Better late than never. I didn’t trust myself notching all the tray dividers on the table saw, so it was a perfect job for the laser cutter.
Each tray got a wipe-down of paste wax on the bottoms and sides for a smooth ride in and out of the box. The drawers fit so snugly that they give a little owl “hoot” when pushing them back in; the escaping air has to pass over the tops of the sample compartments, in effect creating a type of whistle.
Brass hardware keeps everything together. Even though I wanted to use nickel hardware, I was kind of forced to use brass hardware since I couldn’t find the handles I wanted in nickel. Lisa’s keeps the collection secure with an antique brass lock.
The box was finished with Dark Walnut stain and two layers of semi-gloss poly. Before applying the poly, I cut out stencils on the Cameo for each side of the box and applied a quick spray of rattlecan white.
For maximum personalization, I created a name plate so that there would be no question or confusion as to who owned the box, and what was inside.
Lessons Learned
When working with plywood, if I’m making something nice as a gift, I need to either apply edge banding to the exposed plywood edge, or paint the whole box. I finish the plywood surface because I wanted to give a ‘finished wood’ look, but the exposed ply edges really take away from the whole aesthetic.
Also, I got to use my plate joiner for a practical project, which was fairly easy and fun.